
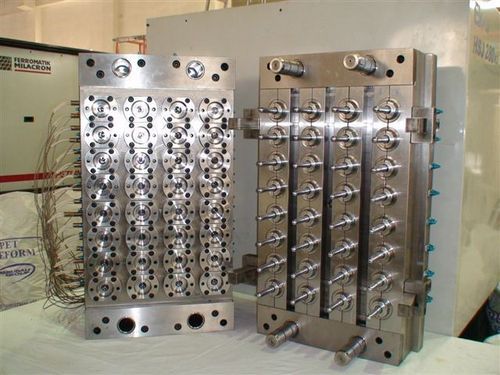
Hot runner molds are used to manufacture PET preforms. Injection systems with temperature control sections and low friction heat are required since PET has a stable time after melting and high melting point, and the actual weight of the plastic should be 2/3 of the one-shot amount of machine injection. Recyclable materials should be no higher than 25%, and they should be thoroughly dried before use.
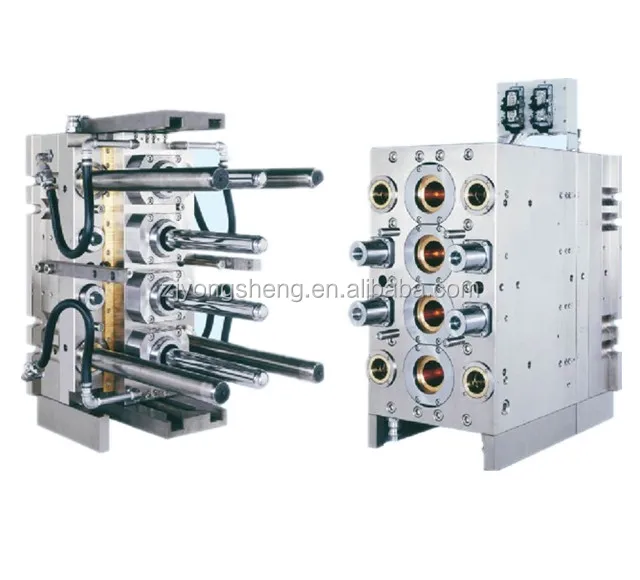
It requires drying at 150 ☌ for at least four hours, generally 170 ☌, over three to four hours, before processing.

PET loses molecular weight when moisture levels exceed the limit the product turns color and becomes brittle. Also, due to their presence, PET has a phospholipid-based structure. Plastic Processingĭue to its lipid-related nature and its hydrophilicity, PET pellets are very sensitive to water at high temperatures. In this situation, the fluidity of the melt is often affected mainly by pressure. As of today, GF-PET is the most popular polymer among customers, which is mainly used in preform injection.Ĭonsequently, the properties of PET in a liquid state are much better, and pressure is more important than temperature in terms of viscosity. Polyethylene terephthalate (PET) is a naturally occurring thermoplastic polymer commonly used in plastic products. With this service, everything you need to be made here can be achieved in the same location. With a comprehensive set of plastic preform mold manufacturing capabilities, we manufacture a broad range of molds in a comfortable working environment.Īs well as our preform available here in our facility, the products can be made right here, or we can create a customized preform mould made from PET for you, to effectively produce your desired packaging. It is the dedicated and experienced workforce of Topworks specializing in more than one division to ensure the design and build of moulds to create unique features tailored to diverse kinds of plastic PET preforms. Whatever your requirements may be, Topworks has the ability to produce a complete set of PET preform moulds promptly, with accuracy, at an affordable price, no matter how detailed or intricate.īesides the ability to design and assemble the PET preform mould according to the customer’s specific needs and the capability to make each PET preform according to the customer’s requirements, it is also possible to print each PET preform with a particular design. In this way, our company has developed a significant amount of expertise and knowledge that enables customers to be assured of receiving the highest level of service, efficiency, and dedication in preform moulding.
